News & Insights
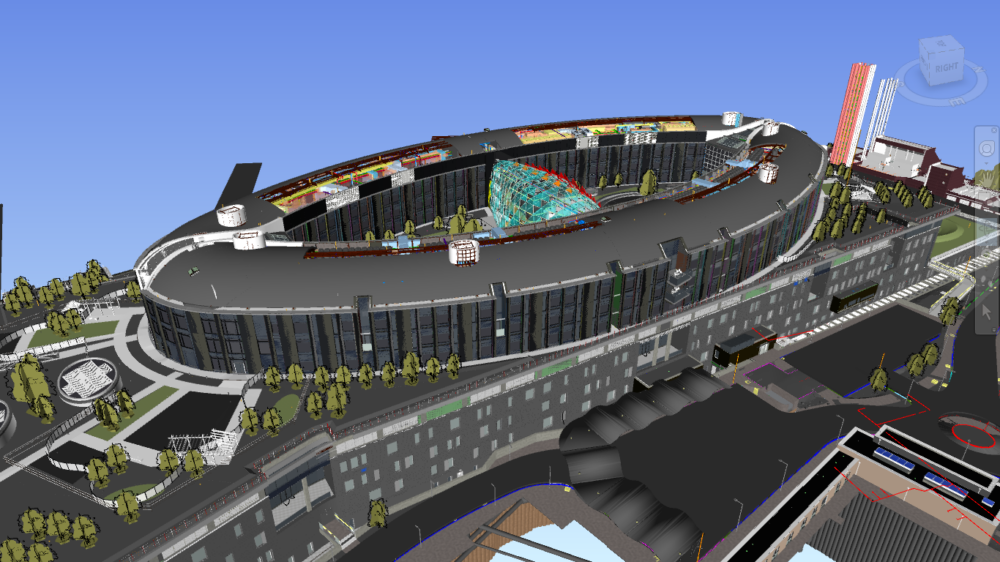
Mercury adds a 4th dimension to its BIM models with Synchro
Mercury has adopted Synchro to integrate the project schedule with the construction model. The introduction of the 3D model as a primary source of project information has revolutionised data representation and management in the construction industry. Recent technological advancements have resulted in the ability to introduce a 4th dimension into the model – time.
Synchro is now being used across three business units Enterprise Data Centres, Healthcare & Hyperscale Data Centres, with projects being delivered in Ireland, France, Germany, Spain, Poland and Italy.
With Synchro, data is added to components to build detail as projects progress. The information is stored in the cloud where it can be exported to various other applications like Power BI, site tracking apps and the HoloLens – mixed reality smartglasses used by Mercury to position holographic images of BIM models in the real world.
“By linking the 3D model to the programme, we can create a visual representation of the construction sequence allowing for better collaboration and engagement with project stakeholders. We can also use this 4D model to track progress and plan the works ahead more accurately. It’s big data enabling us to make informed, real-time decisions”, says Barry Boylan, Planning Manager for Mercury’s Healthcare Business Unit and the team leader of the Synchro project.
“4D scheduling removes some of the uncertainty during the pre-construction stage of projects. We can anticipate clashes and optimise project plans, helping to eliminate sequencing issues before even commencing on site.
“With quantities from the model linked to time in the programme we know when and where materials are required, streamlining procurement and allowing for ‘just in time’ deliveries. From a commercial perspective a 4D model improves the accuracy of cost plans by having known quantities overtime while also assisting with payment applications through accurate as-built drawings.
“For the onsite team the use of 4D visualisations and data output tools like Bi leads to a greater understanding of the plan and less ambiguity on the progress” explains Barry.
Digital Edge
Synchro is an initiative of the ‘Digital Edge’ pillar from Mercury’s Beyond50 strategy. The core goal of this pillar is to deliver a mobile, integrated digital backbone for back office and frontline workers from design through to operations that drives our digital project delivery to the edge. Read more about innovation in Mercury here.
OUR BEYOND50 STRATEGY DESIGN, QUALITY & INNOVATION