Nachrichten und Einblicke
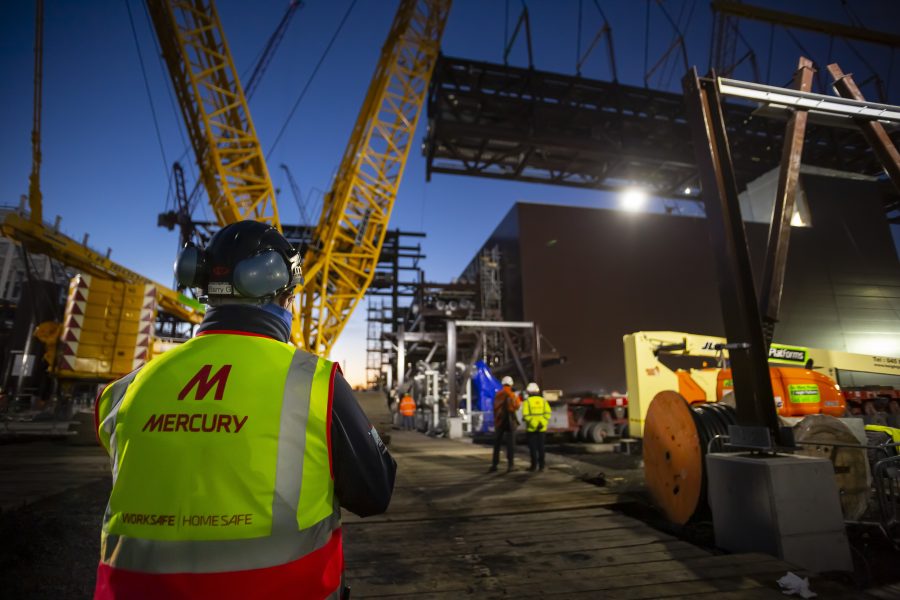
Construction Management the Mercury Way: An Autodesk Case Study
At Mercury, we focus on delivering our clients vision through leading edge construction solutions. Pushing to go beyond their duty means Mercury turns clients into partners and builds strong relationships that thrive. Mercury’s digital construction journey began two years ago with the data centre sector of the business. As the company had grown, the team adopted lots of different technology solutions for their projects and they lacked a standardised approach to implement a connected construction journey. “Our company grew very quickly and added a number of projects to our portfolio. This meant that we began using several different platforms and methodologies across different projects and regions. It soon became obvious to us that a more standardised approach could improve our efficiencies and give us greater results,” reflects Aisling Goff, Business Unit Quality Manager for Mercury’s data centre business unit.
The business unit decided they would adopt one solution for all of their projects moving forward. The objective was to create a more unified and standardised approach to delivering projects for all of their clients. In the first instance, the team surveyed their employee groups to get an understanding of how technology could help them deliver better outcomes in their role. “We ran a series of surveys with our staff to get their feedback on all the different software they were currently using – asking them for the pros and cons in each case. We received input from colleagues in a range of roles, from engineers to document controllers,” says Aisling.
Redefining our industry through standardisation
To further develop their technology roadmap, the data centre business unit team reviewed their project pipeline to evaluate incoming work and cost out their technology requirements accordingly. Ronnie Christie, Business Unit Manager, knew that using technology in a smarter way could better support the team to create continuity. Ronnie says: “We recognised that different sites within a division were reporting differently to the directors and their clients so a big ask of the technology solution we chose was something that could help us standardise our reporting mechanisms.”
When it came to choosing a technology solution, Mercury used Autodesk Construction Cloud’s BIM 360 platform for the first time four years ago on one of their data centre projects. The team initially used the solution for document control and generating snag lists on the project.
Aisling reflects: “When we used BIM 360 for the first time, we had to make sure the client was happy with the software and realised the benefit of using it.” After initially using the solution on one data centre project, Mercury then decided to use it on a new build project that spanned the entire construction phase. The team made use of more of the functionality available – such as workflows for daily reporting, commissioning, permits, check sheets as well as tracking labour and site numbers too. “When we used BIM 360 on our second data centre project, we were impressed with the additional functionality. It allowed us to create clearer workflows for RFIs and submittals alongside a whole range of project activities,” says Aisling.
Making BIM 360 part of the Mercury Way
It was during this project that the Mercury team decided to mandate using BIM 360 on all projects in the future. “We knew that we’d need to approach our BIM 360 rollout to the business in a slow and structured way,” states Aisling. “We got the basics working really well on our first project, and it was only after this that we introduced more functionality to the team on the next project to ensure a smooth transition to the wider team.”
When it came to implementing the technology, the team ensured that employees were thoroughly supported through a comprehensive learning and development strategy. They ran training sessions for teams and individual employees and also created peer mentoring sessions for individuals to learn from each other, with the help of technology champions for the platform. The company also created standard operating procedures for using BIM 360, user guides and shared best practice through their internal skills hub.
“Our colleagues responded really well to the training and learning opportunities made available to them during the rollout stage,” says Ronnie. “For us, peer-to-peer training was key. Our business has expanded dramatically in the last few years due to growth across the unit and we have a really talented bunch of people with great expertise in using digital construction solutions. They were instrumental in strengthening the team’s understanding and use of BIM 360.”
Creating insights from information
For Mercury, when it comes to integrating technology into their business, the team have focused on using the data they capture on projects in a richer way to develop better project insights. Aisling says: “We’ve integrated BIM 360 with Power BI to export data on quality, health and safety. We were unable to get this visibility before. Now we can draw greater insights from our projects to better manage risk, cost and quality.”
Better insights captured from project data can not only improve the construction process, but it can support the health of a business and improve the employee experience. “When new colleagues join and work with existing teams on different projects, they understand fully what processes they need to follow and what information we capture to measure our performance,” says Ronnie.
Collaborating across the supply chain happens within Autodesk Construction Cloud’s BIM 360 platform. “We now use BIM 360 to communicate formally with all of our project stakeholders,” says Aisling. “It’s where all project communication takes place and acts as a central source of truth for Mercury. Everyone uses BIM 360 – from a Quality Assurance team member or a Document Controller in the office to a supervisor using daily reports on site or a Project Manager overseeing daily activity.”
For me, the transparency [from BIM 360] has been transformative. Everything is real and things are no longer open for interpretation as project data is visible for everyone.—Aisling Goff, Mercury
Using one central source of truth in the form of a common data environment has enabled Mercury to empower their teams with full visibility of the status of all their projects. “All submittals and RFIs go through BIM 360 and our supply chain partners use the solution in the field to report on health, safety and quality. We also use the solution to manage our client teams; that can range from resolving questions that need clarification, verification, and design workflows. It works really well for us as we use the solution to manage up and down as well as across teams,” remarks Aisling. This has improved communication and collaboration between project stakeholders resulting in a dramatic reduction in the amount of miscommunication and lost documentation.
Getting the right tools in the right hands
For Aisling and Ronnie, the benefits of working more digitally are twofold – not only do their teams deliver a better client experience, but they are also able to ensure they are set up for success from the very beginning of a project. Ronnie says: “All of our projects are structured in the same way now using BIM 360. This means our colleagues can move between projects easily; they know what to expect when they join a new project team, and the business knows how to set itself up for success.”
Both Aisling and Ronnie agree that their favourite features enable them to use their data in a more meaningful way. Aisling remarks: “If I had to pull out my favourite thing about BIM 360, it would definitely be that it enables us to use the same parameters when it comes to analysing our data. This means we have a standardised way of reporting to use the data better.” For Ronnie, being able to benchmark across teams and see how they are progressing when audit reporting supports him in his role. Ronnie says: “I’m able to gauge how jobs are running in parallel with each other which has been really useful.”
Monitoring adoption has helped Mercury to establish where they need to put more focus. “As a company, we monitor what functionality each project is using in BIM 360 to make sure we’re getting the most out of the technology,” says Aisling. “Our data centre business unit has reached an average 90% KPI score for adoption. We’ve found that the last 10% of adoption in terms of maximising all the functionality usually involves bringing all project stakeholders along and making sure they’re bought into the technology.” This also means Mercury can work collaboratively across their individual business units with their teams to share best practice, learnings and break down siloes.
“We now have much greater predictability and insights on our projects,” says Ronnie. Mercury has also fostered greater collaboration across their business units and wider company whilst standardising the data sets and data types they capture. “For me, the transparency has been transformative. Everything is real and things are no longer open for interpretation as project data is visible for everyone,” affirms Aisling.
Looking to the future, Mercury plans on ensuring all their teams across the entire company are getting the most from BIM 360 using the functionality available. In addition to this, working in collaboration with their clients, they are promoting the benefits of implementing standardisation and digital workflows within the AEC industry.
This year, Mercury is going through the process of gaining their ISO 19650 accreditation which highlights their ambition to fully utilise the international standards for managing information over the whole life cycle of a built asset using building information modelling (BIM). As a company, they are wholly committed to driving the digital agenda to create a more productive and efficient industry with better insights to deliver improved outcomes for clients and end users alike.
Digital Edge
Our road to technology standardisation forms part of Mercury’s Beyond 50 strategy, sitting under our ‘Digital Edge’ pillar. The goal of Digital Edge is to get the right technology into the hands of our frontline workers who deliver the real value to our clients, pushing digital construction to the edge.
An alternative version of this article originally appeared on Autodesk’s Construction Blog. Click here to read it.