Nachrichten und Einblicke
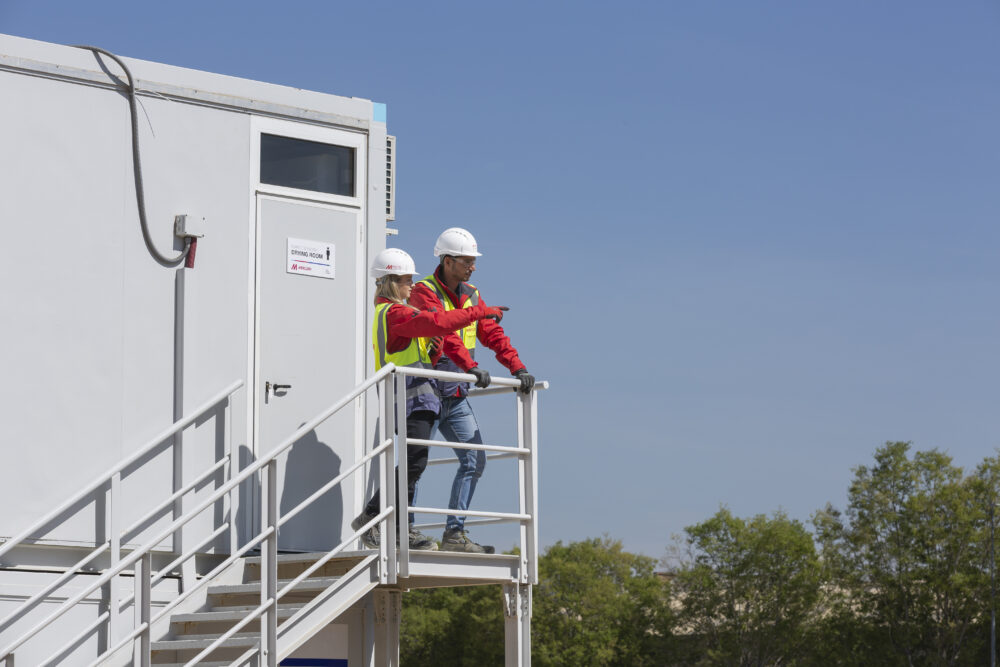
Achieving zero-emission construction sites using innovative approaches
The construction industry, particularly within the European Union, is in the midst of a significant transformation. Triggered by the escalating demand for lower emission standards, plant suppliers have begun to diversify their portfolios with an increased focus on electric and hybrid offerings. This shift holds considerable implications for general contractors, presenting a wide range of opportunities as well as a new set of challenges.
Amid this changing landscape, Balaji Gunaseelan, a Mechanical & Electrical Commissioning Engineer with Mercury, stands as an industry beacon. Recently, Gunaseelan featured as a guest speaker at the Innovatrix’s Design and Development of Zero-Emission Off-Highway Machinery conference in Berlin. His comprehensive expertise and deep understanding of emission reduction complexities in construction projects formed the basis of his address, wherein he provided attendees with an extensive overview of the evolving sector, as it steers towards electrification.
In his presentation, Gunaseelan identified several key trends impacting Mercury, particularly concerning the use of electrical plant systems in data centre projects. He outlined innovative methods that Mercury is implementing to mitigate these challenges, all aimed towards ensuring sustainable and efficient project delivery.
Availability of Electrical Plants
For us at Mercury, immediate access to electrical plants is crucial, especially given the fast-paced nature of the data centre industry. With the ongoing shift towards lower emission standards, leasing this equipment for the duration of a project has become a cost-competitive option compared to diesel equivalents. However, there are often challenges that we are required to mitigate around power supply and availability, which are outlined below.
Power Supply Design and Establishing Infrastructure
In our journey towards zero-emission construction sites, meticulous power supply designs are vital. Our data centre projects typically require a power spectrum of 10 to 100MWs upon completion. Although our clients are capable of sourcing power from grid connections or dedicated substations, the construction phase introduces unique challenges. Critical plant equipment, such as MEWPs, boom lifts, excavators, and scissor lifts, cumulatively demand about 300KW of electricity during a typical data centre project. This demand, when combined with a standard site supply of around 600KW, pushes the total necessary power supply to exceed 1MW (considering the factor of safety).
Data centre projects are often strategically located on the outskirts of cities, adding another layer of complexity to setting up a temporary power supply solution. To mitigate this, we frequently resort to temporary electrical installations, despite their above-market costs. These installations, commissioned at the project’s onset and decommissioned upon its completion, can significantly affect project timelines, and necessitate a sophisticated approach to managing power supply logistics.
Moreover, establishing the infrastructure for a temporary power supply in zero-emission construction sites is not without its challenges. Higher capacity requirements lead to longer lead times, thereby impacting project timelines. However, starting the setup process earlier or deploying additional resources can help mitigate these challenges.
Infrastructure Maintenance
Maintaining high-capacity electrical infrastructure is part of the complexities involved in this shift towards lower emissions. As power demand increases, maintenance requirements and potential downtime rise as well. We rely on specially trained professionals who are certified to handle high-voltage systems, which are crucial for minimising power disruptions.
Limited Grid Access
Assuming the grid supplier can typically meet power demand, limitations arise when local grids cannot support the higher capacity temporary power supply system. Extended approval processes, higher costs, and longer lead times can restrict deployment in certain countries. In response, we’re exploring the use of battery packs as a potential solution to manage power fluctuations.
Oversized Generators
The deployment of multiple chargers on-site often necessitates oversized generators to sustain peak loads, leading to challenges such as higher emissions, increased fuel consumption, and noise pollution. To address this, we at Mercury are exploring battery technology to optimise power generation, reinforcing our commitment to innovative methods and sustainability.
Deployment Restrictions
The availability of equipment and trained specialists adds to the complexities of deploying zero-emission construction sites. But in line with broader industry trends, suppliers are gradually increasing their offerings to meet the growing demand. Collaboration between equipment providers and construction companies is crucial to ensure a readily available supply. Additionally, comprehensive training programs are essential to equip specialists with the necessary skills.
At Mercury, we actively seek to overcome deployment restrictions by collaborating with equipment providers, investing in training programs, and embracing the financial benefits of zero-emission technologies. We are driven to create a sustainable and environmentally responsible construction industry by adopting sustainable practices, maximising equipment availability, and minimising deployment challenges.
RESPONSIBLE BUSINESS – OUR PLANET, OUR DUTY
We believe that we each have a role to play in contributing to the sustainable development of our planet. With this in mind, we have launched Our Planet, Our Duty, our Responsible Business plan. Our Planet, Our Duty is our promise to help create a more sustainable environment around us. It forms one of the foundation blocks of Beyond50, our five year plan to push further and take Mercury beyond our 50th year in business.
Follow us on LinkedIn, Facebook, and Instagram.